
Plastic chips are versatile components used in a multitude of industries. Typically crafted from high-quality polymers, these chips serve as essential parts in medical devices, automotive systems, and consumer electronics. Their inherent flexibility allows for widespread applications but also presents the opportunity for targeted customization to meet specific industry needs.
Exploring the Potential of Plastic Chips
Understanding plastic chips begins with recognizing their materials. These chips can be made from various kinds of plastics such as polyethylene, polycarbonate, and polypropylene. The material selection hinges on the requirements of the application, influencing factors like strength, durability, and chemical resistance.
Across different sectors, plastic chips fill crucial roles. In the medical field, they must exhibit biocompatibility and precision to ensure patient safety and effective device operation. Automotive applications demand superior durability and performance under extreme conditions, while consumer electronics thrive on miniaturization and efficiency. Each industry's unique specifications underscore the importance of customized solutions.
The Need for Customization
Customization isn't merely an added benefit; it's often a necessity. For instance, medical users require biocompatible materials capable of performing intricate functions within tight tolerances. In contrast, the automotive sector looks for robust materials that withstand mechanical stresses and environmental exposure. Consumer electronics emphasize compactness, higher performance, and energy efficiency, demanding innovative designs tailored through precise customization techniques.
Customization Techniques
Choosing the appropriate type of plastic is critical. Factors like required durability, flexibility, heat resistance, and biological inertness guide this decision. Additionally, using advanced tools such as CAD software enhances design precision, enabling rapid prototyping methods which allow quick iterations to refine the final product.
Different manufacturing processes cater to distinct production needs. Injection molding, suitable for high-volume production, provides consistent quality at scale. Conversely, 3D printing excels when crafting intricate designs in smaller batches, facilitating detailed and complex geometries not achievable with traditional methods.
Benefits of Tailored Plastic Chips
Tailoring plastic chips enhances both performance and longevity by meeting exact operational requirements and extending the life span of the final product. Furthermore, cost efficiencies arise from reduced waste due to precise customization and optimized designs resulting in lower production expenses. This blend of performance improvement and cost reduction illustrates the tangible advantages of bespoke plastic solutions.
Case Studies and Success Stories
Real-world examples demonstrate the transformative impact of custom plastic chips. Medical devices benefit significantly from personalized components crafted from biocompatible materials, improving function and patient outcomes. In consumer electronics, specially designed plastic chips contribute to the creation of sophisticated gadgets boasting higher efficiency and smaller sizes, enhancing user experiences worldwide.
Future Trends in Plastic Chip Customization
Continuous advances in material science are expanding the horizons for plastic chip customization. New polymers and composites offer enhanced functionalities, including sustainable and eco-friendly options addressing environmental concerns. Innovative manufacturing techniques driven by AI and machine learning are revolutionizing design optimization, predicting best-fit models with unprecedented accuracy. Emerging technologies in additive manufacturing further augment capabilities, broadening the scope of what’s possible.
Getting Started with Customization
Embarking on the journey to customize plastic chips necessitates selecting the right partner. Key attributes include experience, technological capability, and a collaborative approach. Questions centered around their expertise, past projects, and flexibility in handling specific demands provide valuable insights into their suitability.
The process from concept to final product involves several steps including requirement analysis, iterative designing, rigorous testing, and continuous feedback integration. Each phase ensures the resultant chips align perfectly with intended applications, delivering optimal performance.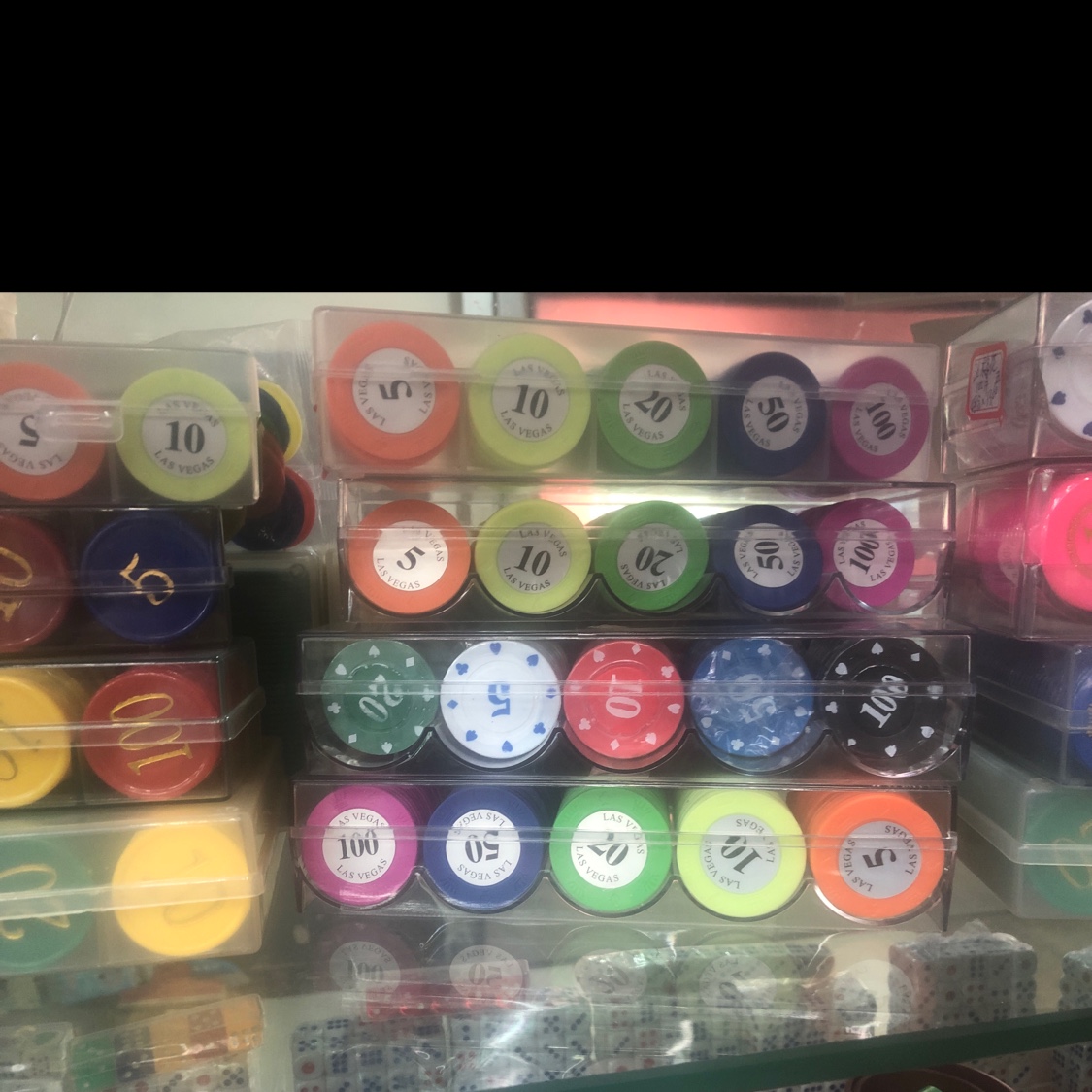